Safety Precautions For Anti-corrosion Steel Pipe Construction
3PE anti-corrosion steel pipe spraying technology, most domestic 3PE anti-corrosion steel pipe production technology adopts the production and processing technology of “epoxy powder spraying, adhesive and polyethylene lateral extrusion, winding rolling”, because the powder and electrostatic thermal spraying method does not require rolling system, thus solving the problem of thin weld coating of spiral structure welded steel pipes, saving a large amount of plastic extruders and other mechanical equipment on the production line, and reducing production energy consumption.
Specific construction: The steel pipe after shot blasting and rust removal is heated to 210°C to 220°C at a moderate temperature, and the epoxy powder is still in a molten state. The adhesive and PE are extruded into thin sheets with an extruder, sprayed and wrapped around the steel pipe, and then flattened with a roller; the epoxy powder is in powder form, and the adhesive and PE are in granular form, and only electrostatic spraying and plasticization can be used Extrusion wrap.
There are many reasons for the bending of steel pipes, such as the thermal impact of the welding seam, eccentricity during forming, compression force, imbalance of bending force, etc. But fundamentally speaking, bending is the result of internal stress in the steel pipe. Simply put, bending is stress imbalance. So, does a straight steel pipe have no internal stress? no. Straight steel pipes also have internal stress, but the internal stress of straight pipes is smaller.
What is internal stress? Temperature, an interaction force between molecules that causes deformation due to the influence of external forces. When steel pipes are formed and welded, they will also be affected by external forces such as welding temperature and forming bending, resulting in internal stress. The cross-section of the steel pipe is an annular shape, and two basic stresses will be generated in this annular area: a force parallel to the annular shape and a force perpendicular to the annular shape. Parallel stresses will cause the tube to become out of round; vertical stresses will cause the tube to bend. Therefore, there is a cold diameter expansion process in the production process of straight seam steel pipes. The purpose is to eliminate the internal stress of the steel pipe and increase the strength of the straight seam steel pipes.
The pipe that needs to be straightened is fed into the lower roller of the straightening machine from the feeding device at the left end (or right end) of the machine. The upper roller moves downward to press the pipe and stop after reaching the corresponding position. The upper and lower rollers are respectively inclined at a certain angle with the axis of the straightened pipe. The hyperbolic generatrix of the rollers matches the outer diameter of the pipe and forms an envelope shape.
The three upper rollers are pressed against the pipe under the action of their respective hydraulic cylinders, and the two lower rollers are driven to rotate by their respective hydraulic motors, driving the pipe to both rotate around the axis and move along the axial direction. Changing the rotation direction of the hydraulic motor can change the rotation direction and axial movement direction of the pipe to achieve reversible straightening. The straightened pipe is then sent to the material rack through the discharging device at the other end. For pipes with large local bending deformation, the punches at both ends can be used to perform partial straightening first, and then perform overall straightening.
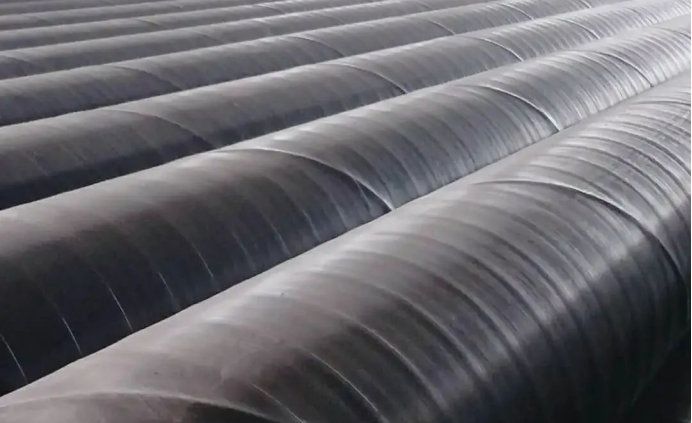
댓글을 남겨주세요
토론에 참여하고 싶으신가요?자유롭게 기여해 주세요!