Carbon steel material for Hydrogen sulfide corrosion applications
Hydrogen sulfide H₂S is an inorganic compound that is colorless, flammable, soluble in water acid gas, hydrogen sulfide corrosion refers to the oil and gas pipeline containing a certain concentration of hydrogen sulfide (H2S) and water corrosion. H₂S dissolves in water and becomes acidic, leading to electrochemical corrosion and local pitting and perforation of pipelines. The hydrogen atoms generated in the corrosion process are absorbed by the steel and enriched in the metallurgical defects of the pipe, which may lead to the embrittlement of the steel and the initiation of cracks, leading to cracking. The pipeline and equipment of acid oil and gas fields containing H₂S have appeared many times sudden tearing or brittle fracture, welding zone cracking and other accidents, which are mainly caused by hydrogen-induced cracking (HIC) and sulfide stress cracking (SSC).
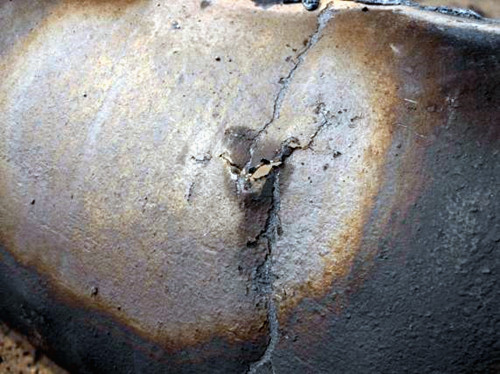
The factors affecting the corrosion of H₂S include hydrogen sulfide concentration, PH value, temperature, flow rate, carbon dioxide and chloride ion (C1-) concentration, etc. A wet hydrogen sulfide stress corrosion environment is constituted if the following conditions are met:
- Medium temperature is not greater than 60+2P ℃, P is the medium gauge pressure (MPa);
- B partial pressure of hydrogen sulfide is not less than 0.35mpa;
- The medium contains water or the medium temperature is lower than the dew point temperature of water;
- Medium with PH less than 9 or cyanide.
The results show that for the alloy steel when the strength or hardness of the steel is the same, the microstructure of uniform distribution of small spherical carbides can be obtained by high temperature tempering after quenching, and the resistance to H2S corrosion is better than that after tempering. The shape of inclusions also matters, especially the shape of MnS, because MnS are prone to plastic deformation at high temperatures, and the sheet MnS formed by hot rolling cannot be changed during subsequent heat treatment.
Elements Mn, Cr and Ni are added to the carbon steel to improve the hardenability, especially Ni. It is generally believed that Ni element is beneficial to the toughness of alloy steel, but the hydrogen evolution reaction overpotential of Ni steel is low, the hydrogen ion is easy to discharge and reduce to accelerate the hydrogen precipitation, so the resistance of Ni steel to sulfide stress corrosion is poor. In general, carbon steel and alloy steel should contain less than 1% or no nickel. Elements such as Mo, V, Nb, etc. that form stable carbides in steel.
ISO 15156-2, ISO15156-3 or NACE MR0175-2003 have limited the environmental conditions to avoid the occurrence of stress corrosion. If these conditions are not met, HIC and SSC tests shall be performed, and other relevant standards shall be met. The American Corrosion Institute (NACE) MR-01-95 states that to prevent sulfide stress corrosion cracking (SSCC), ordinary steel (nickel content less than 1%) with a hardness below Rockwell HRC22 or tempered chrome-molybdenum steel with nickel content less than HRC 26 shall be used.
In addition, there are other restrictions:
- Impurities in steel: sulfur ≤ 0.002%, P≤0.008%, O≤ 0.002%.
- Hardness is not more than 22HRC, yield strength is less than 355MP, tensile strength is less than 630MPa
- The carbon content of steel should be reduced as much as possible under the condition of satisfying the mechanical properties of steel plate. For Low carbon steel and carbon-manganese steel: CE≤0.43, CE=C+Mn/6; For low alloy steel: CE≤045 CE=C+Mn/6+(Cr+Mo+V)/5+(Ni+Cu)/15
Steel plate:SA387 Gr11(HlC), SA387 Gr12(HlC), SA387 Gr22(HlC), SA516 Gr65(HlC), SA516 Gr70(HlC);
Steel pipe: API 5CT H40, J55, L55, C75(1,2,3), L80(type 1), N80(type Q/T), C95(type Q/T), P105, P110 Q/T); API 5L grade A, grade B, X42, X46, X52; ASTM A53, A106(A, B, C)
The avaiable carbon Steel pipe and plate for H₂S application
اترك رداً
تريد المشاركة في هذا النقاششارك إن أردت
Feel free to contribute!