Esistono molti metodi di isolamento per i tubi in acciaio anticorrosione
Il tubo d'acciaio anticorrosione è un nuovo tipo di tubo d'acciaio che, dopo il trattamento anticorrosione, può efficacemente prevenire o rallentare la corrosione delle reazioni chimiche o elettrochimiche durante il trasporto e l'uso; tuttavia, essendo un eccellente tubo d'acciaio anticorrosione, si prega di prestare attenzione quando lo si utilizza; tenerlo al caldo, soprattutto nel freddo inverno,
Esistono infatti diversi metodi di isolamento per i tubi in acciaio anticorrosione, tra cui i rivestimenti isolanti, l'avvolgimento di materiali anticorrosione intorno ai tubi in acciaio anticorrosione e il riempimento e l'isolamento dei tubi in acciaio anticorrosione. In particolare, si tratta di:
1. I tubi d'acciaio anticorrosione sono isolati mediante rivestimenti termoisolanti, ossia: utilizzando perlite espansa, pietra di rana espansa, polvere di amianto, fibre di amianto, clinker di diatomite e altri materiali amorfi termoisolanti, quindi aggiungendo cemento, acqua di vetro, legante refrattario (come l'argilla) o coagulante (come il fluorosilicato di sodio), quindi aggiungendo acqua in una certa proporzione e mescolando in modo uniforme per formare una boiacca, oppure utilizzando questi materiali isolanti a mani nude o applicandoli sui tubi in acciaio anticorrosione con degli strumenti, Questo metodo di isolamento per i tubi in acciaio anticorrosione è chiamato anche rivestimento isolante.
2. I tubi in acciaio anticorrosione sono isolati mediante l'avvolgimento di materiali isolanti, cioè direttamente con materiali isolanti come feltro di scorie, feltro di lana di vetro, corda di paglia, corda di amianto o nastro di cotone, in modo che non ci si debba preoccupare che il tubo in acciaio anticorrosione sia congelato e incrinato. Non influisce sull'utilizzo del tubo in acciaio anticorrosione.
3. Il tubo in acciaio anticorrosione viene riempito con materiale termoisolante, ovvero, quando il materiale termoisolante è un materiale a blocchi, può anche essere riempito con materiale termoisolante; tuttavia, durante il processo di costruzione, l'anello di supporto in acciaio rotondo viene fissato sulla parete del tubo, e il suo spessore e l'isolamento Lo stesso strato, quindi avvolgere l'anello di supporto con ferro, alluminio o filo spinato, e poi isolare con materiale termoisolante; riempimento del materiale; il metodo di riempimento può anche utilizzare blocchi rigidi prefabbricati a forma di arco in materiale poroso come struttura di supporto, con una distanza di circa 900 mm, in base alla forma e alle dimensioni dello strato isolante della conduttura, la rete metallica piatta intrecciata con filo spinato viene tagliata e la macchina avvolgitrice viene trasformata in un cerchio, in modo che la lana di scorie copra l'anello di supporto, e poi il guscio protettivo metallico viene utilizzato per riempire la struttura isolante.
4. Inoltre, possiamo anche utilizzare il trattamento di isolamento termico prefabbricato dei tubi in acciaio anticorrosione per mantenere l'isolamento termico. I materiali principali dei prodotti prefabbricati per l'isolamento termico sono il cemento espanso, l'amianto, la terra di diatomee, la lana di scorie, la lana di vetro, la lana di roccia, la perlite espansa, la vermiculite espansa, il silicato di calcio, ecc.
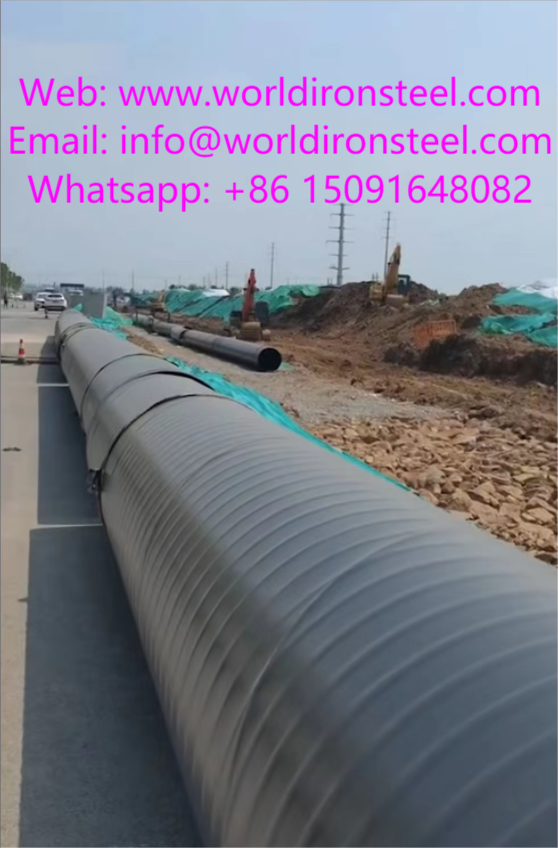