Er zijn veel isolatiemethoden voor corrosiewerende stalen buizen
Anti-corrosie stalen buis is een nieuw type stalen buis, na anti-corrosie behandeling, kan het effectief voorkomen of vertragen van de corrosie van chemische of elektrochemische reacties tijdens transport en gebruik, maar het is een uitstekende anti-corrosie stalen buis, let dan op bij het gebruik ervan, houd het warm, vooral in de koude winter,
In fact, there are many insulation methods for anti-corrosion steel pipes, including coating insulation coatings, wrapping anti-corrosion materials around anti-corrosion steel pipes, and filling and insulating anti-corrosion steel pipes. Specifically, they are:
1. Anti-corrosie stalen buizen worden geïsoleerd door coating warmte-isolerende coatings, dat wil zeggen: met behulp van geëxpandeerd perliet, geëxpandeerde kikkersteen, asbestpoeder, asbestvezels, kiezelgoer klinker en andere amorfe warmte-isolerende materialen, en voeg dan cement, waterglas , vuurvast bindmiddel (zoals klei) of stollingsmiddel (zoals natriumfluorsilicaat) toe, voeg dan water toe in een bepaalde verhouding en meng gelijkmatig om een slurry te vormen, of gebruik deze isolerende materialen op blote handen of breng ze aan op anticorrosiestalen buizen met gereedschap , Deze isolatiemethode voor anticorrosiestalen buizen wordt ook coatingisolatie genoemd.
2. Dat wil zeggen, direct omwikkeld met isolatiemateriaal zoals slakkenvilt, glaswolvilt, strokoord, asbestkoord of katoenen tape, zodat je je geen zorgen hoeft te maken dat de stalen anticorrosiepijp bevriest en barst. Heeft geen invloed op het gebruik van de corrosiewerende stalen buis.
3. De corrosiewerende stalen buis is gevuld met thermisch isolatiemateriaal, dat wil zeggen, wanneer het thermische isolatiemateriaal een blokmateriaal is, kan het ook worden gevuld met thermische isolatie; echter, tijdens het bouwproces wordt de steunring van rond staal op de buiswand bevestigd, en de dikte en isolatie Dezelfde laag, wikkel dan de steunring in met ijzer, aluminium of prikkeldraad, en isoleer het vervolgens met warmte-isolerend materiaal; materiële vulling; de vullingsmethode kan ook geprefabriceerde stijve boogvormige blokken van poreus poreus materiaal als ondersteunende structuur gebruiken, met een afstand van ongeveer 900mm , volgens de vorm en de grootte van de pijpleidingsisolatielaag, wordt het vlakke geweven netwerk van het prikkeldraad gesneden, en de windende machine wordt verwerkt tot een cirkel, zodat de slakkenwol de steunring bedekt, en dan wordt de metaalbeschermende schil gebruikt om de isolatiestructuur te vullen.
4. Daarnaast kunnen we ook gebruik maken van geprefabriceerde thermische isolatie behandeling van anti-corrosie stalen buizen om thermische isolatie te behouden. De belangrijkste materialen van geprefabriceerde thermische isolatieproducten zijn schuimbeton, asbest, diatomeeënaarde, slakkenwol, glaswol, steenwol, geëxpandeerd perliet, geëxpandeerd vermiculiet, calciumsilicaat, enz.; geprefabriceerde buisisolatiestructuren, meestal met een diameter van DN ≤ 80 mm, met behulp van een halfronde schaal, zoals DN ≥ 100 mm, met behulp van waaiervormige tegels (gebogen tegels) of trapeziumvormige tegels.
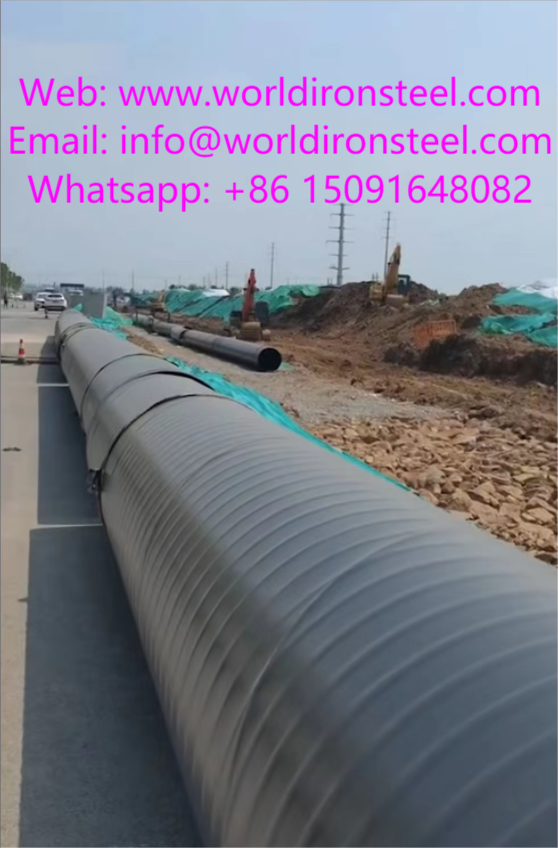