How is the heat exchange tube connected with the tube sheet?
The connection form of heat exchange tube and tube plate mainly includes expansion, welding, expansion welding, etc. The strength expansion joint refers to the expansion of the sealing performance and tensile strength of the connection between the heat exchange tube and the tubesheet. It relies on the plastic deformation of the tube end to withstand the pulling force. The residual stress after the expansion of the tube will gradually weaken when the temperature increase so that the sealing performance and strength of the connection between the tube and the tube sheet will decrease. Therefore, the strength expansion is suitable for the design pressure is less than or equal to 4MPa, the design temperature is less than or equal to 300℃. The strength expansion should not be used in the case of severe vibration, large temperature difference, or obvious stress corrosion during operation.
When expanding the tube, the hardness of the tube should be lower than that of the tube sheet. The gap between the pipe and the pipe and the smoothness of the pipe affects the quality of the expanding pipe. The rough surface of the pipe hole can produce a large friction force and is not easy to pull off, but it is easy to produce leakage. The surface of the pipe hole is strictly prohibited to have a longitudinal through the groove. The smooth surface of the tube hole is not easy to leak, but easy to pull off. Generally, the surface roughness is required to be less than or equal to 12.5μm. There are two kinds of pipe holes: holes and annular grooving, the former as shown in figure (a) below, and the latter as shown in Figure (b) and (c) below.
After grooving, the steel tubes are squeezed into the grooves when expanding, which can improve the pull-off resistance and enhance the sealing performance. The number of annular slots in the tube hole depends on the thickness of the tube plate. Generally speaking, a slot is opened when the thickness is less than 25mm, and two slots are opened when the thickness is greater than 25mm. When the tube plate is thick or to avoid gap corrosion, the structure shown in the following figure (d) can be used, the composite tube plate and heat exchange tube can also be expanded, when the cladding is greater than or equal to 8mm, should be in the groove on the tube hole, the structure is shown in the following figure (e).
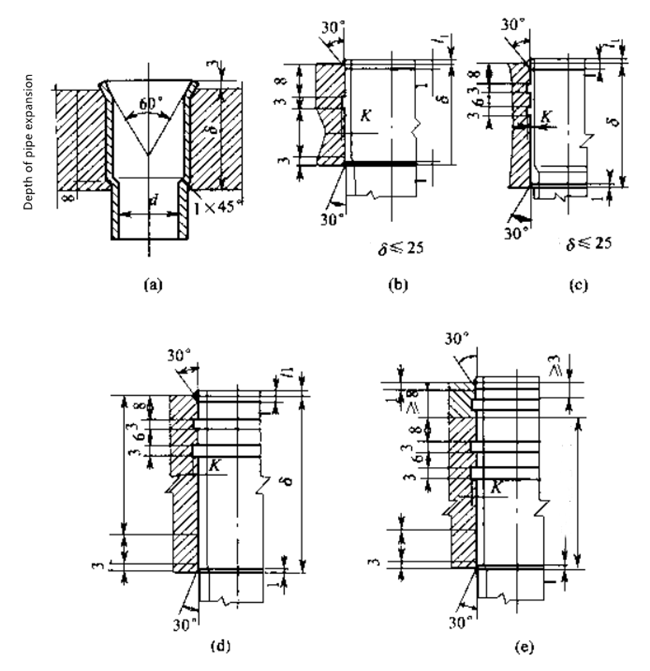
Strength welding refers to ensure the sealing performance and tensile strength of the heat exchange tube and tubesheet connection, is the most widely used tubesheet connection types. Strength welding manufacturing is simple, the tensile ability is strong, such as welding part failure, can be secondary repair welding, more convenient heat exchange tube. The use of strength welding is not limited by pressure and temperature, but it is not suitable for the occasion of large vibration or gap corrosion. The general form of strength welding is shown in figure (a) below. In order to avoid liquid accumulation around the pipe end, the structure as shown in figure (b) below is often used. The structure as shown in figure (c) below is generally used in the situation where the tubesheet is stainless steel.
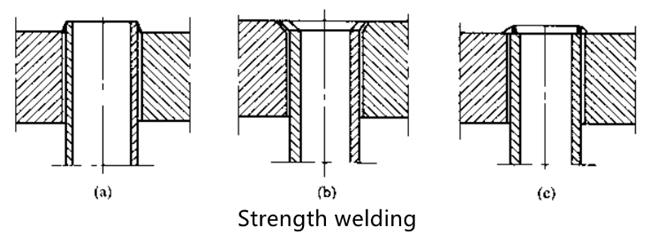
The sealing performance of the joint between tube and tube plate is required to be high, or there is clearance corrosion, withstand severe vibration and other occasions, single expansion or welding can not meet the requirements, the combination of the two can provide enough strength and good sealing performance. The combination of expansion and welding can be divided into two kinds according to the expansion and welding sequence: expansion and welding after expansion. The general expansion method will inevitably have oil stains in the joint gap, which will be welded after expansion. These oil stains and the air in the gap will reduce the weld quality.
Weld before expansion, will cause damage to the weld. At present, there is no uniform provision for the choice of the two orders. In the actual engineering, such as expansion after welding, before welding should be clean oil; If the first welding after expansion, should be a limit to the expansion position of the tube end, generally to control from the surface of the tube plate 15mm above the scope of expansion. The first expansion and then welding generally adopts the form of strength expansion and seal welding. The strength expansion ensures the sealing performance of the tube and tubesheet, providing enough tensile strength, and the seal welding further ensures the sealing performance of the tube and tubesheet. The structure is shown in the figure (a). Strength welding ensures the sealing performance of the tube and tubesheet, providing sufficient tensile strength, and sticking expansion eliminate the gap between the tube and the tube hole to ensure the sealing performance. The structure is shown in figure (b).
In essence, explosive expansion is also a kind of strength expansion, the latter usually adopts roller expansion, the former uses the explosive in a very short period of time to produce high-pressure gas shock wave to make the pipe firmly attached to the tube hole. High explosive expansion and connection efficiency, no need of lubricating oil, easy to weld after expansion, large tensile strength, small axial elongation and deformation.
Explosive expansion is suitable for thin wall tubes, small diameter tubes and large thickness tube sheet expansion, heat exchange tube end leakage, mechanical expansion is difficult to repair the occasion.
Leave a Reply
Want to join the discussion?Feel free to contribute!