Connection Of Polyurethane Insulated Pipes
Polyurethane insulation pipe, which is the full name of high-density polyethylene plastic outer protective polyurethane foam prefabricated direct-buried insulation pipe, is formed by connecting the working medium pipeline, polyurethane insulation layer and polyethylene plastic outer protective pipe that transports the medium through the equipment. Forming. Polyurethane insulation pipes are widely used. It has the following advantages: good thermal insulation performance, low heat loss, only 25% of traditional pipes, long-term operation can save a lot of energy, and greatly reduce energy costs; it has strong waterproof, corrosion resistance and high mechanical strength The strength can meet the non-compensated thermal stress requirements of direct burial. With a service life of more than 30 years, the correct installation and use can make the maintenance cost of the pipe network very low; no additional pipe trench is required, it can be directly buried underground, the construction is convenient and fast, and the total cost is low; the alarm system can be set up and automatically detected Pipe network leakage failure, automatic alarm, high stability; the product is directly buried underground, which is conducive to environmental beautification and urban planning. There are two connection methods for polyurethane insulation pipes:
(1) heat shrinkable tape
When using this connection method, the joint sleeve adopts a polyethylene sleeve of the same material and density as the prefabricated insulation pipe sleeve. The polyethylene joint sleeve is connected with the main pipe and sealed with heat shrink tape to ensure the watertightness of the joint. Then, the joint is foamed at the foaming hole on the joint sleeve, and after the foaming is completed, the foaming hole is sealed by repairing or hot-melt welding with high-density polyethylene.
(2) Electric heating sleeve
This welding method needs to pre-embed the resistance wire sleeve, and then use a strap to firmly bind the hot-melt sleeve to the outer tube, then turn on the power to start welding, the welding time needs to be set in advance, the welding will stop after the automatic power off, the sleeve Once the barrel has cooled completely, remove the belt. With this connection method, the solder joints are very strong and easy to handle.
Also note these:
1. During construction, the interface of the protection pipe should not be soaked by rainwater or groundwater. If the joint is accidentally immersed in water, it should be dried before welding the elbow.
2. The elbows of polyurethane direct buried insulation pipes are divided into finished elbows and basic elbows. The insulation layer and anti-corrosion layer are prepared when the elbow leaves the factory. Pay attention to this kind of elbow when welding, and do not directly contact the flame to prevent the insulation layer and anti-corrosion layer from being damaged; the basic elbow can be directly welded to make the insulation layer and anti-corrosion layer. Usually, after welding, there will be specialized technicians to make insulation layer and anti-corrosion layer for the pipeline.
3. After the elbows and joints are welded, the pipeline should be pressure tested to ensure the tightness of each welded joint.
4. Carry out anti-corrosion treatment on the solder joints after testing the air tightness. Since most polyurethane insulation pipes are buried underground after completion, the corrosion resistance and heat preservation of the insulation pipe can be ensured.
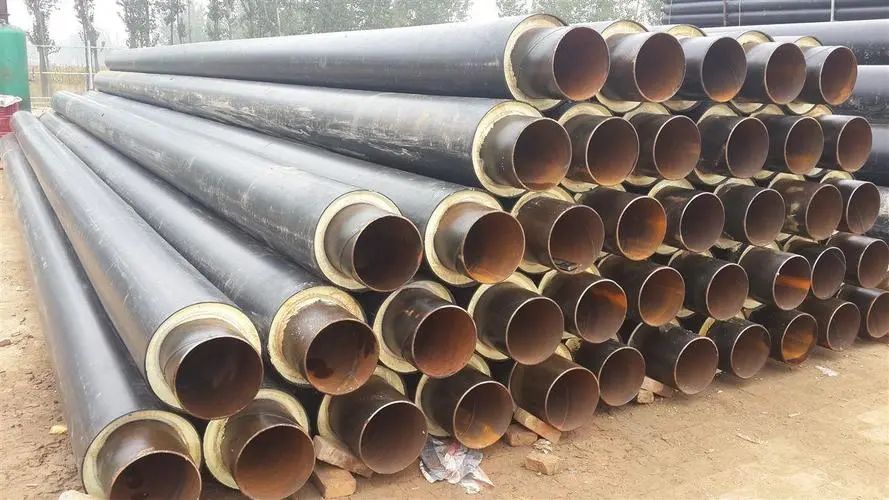
اترك رداً
تريد المشاركة في هذا النقاششارك إن أردت
Feel free to contribute!