Voordelen van kunststof beklede composietpijp
De kunststof-gecoate composietbuis is gemaakt van gelaste stalen buis als basismateriaal en wordt gemaakt door zandstralen chemische dubbele voorbehandeling, voorverwarming, kunststof coating, uitharding, nabehandeling en andere processen. Het heeft uitstekende uitgebreide eigenschappen, sterke mechanische corrosiebestendigheid, goede chemische stabiliteit en waterbestendigheid, en heeft functies zoals corrosiebestendigheid, drukbestendigheid en antibacterieel.
Het wordt over het algemeen niet beperkt door het transportmedium en de plastic coating heeft een sterke hechtkracht met het staal. Coatingmateriaal: Epoxyhars (EP) is geschikt voor de werkomgeving. De stalen buiscoating onder 80 °C heeft een hoge hechting, een hoge hardheid, een goede slagvastheid en een goede weerstand tegen chemische corrosie.
De voordelen van het product zijn de hoge mechanische sterkte, geschikt voor ruwe gebruiksomgevingen; de binnenste en buitenste coatings kunnen metaaloxidatie voorkomen en hebben een goede weerstand tegen chemische corrosie. De coating heeft een sterke hechting, hoge hechtsterkte en goede slagvastheid. Lage coëfficiënt van oppervlakteruwheid en wrijvingscoëfficiënt, goede hechting aan vreemde stoffen; anti-veroudert, lange levensduur.
De met kunststof beklede stalen buis is een nieuw type buismateriaal dat de afgelopen jaren is ontwikkeld. De pijpleiding heeft met succes het verlies als gevolg van corrosie in de pijpleiding verminderd en behoort tot de groene energiebesparende pijpleiding. De drukvastheid, trekvastheid, corrosiebestendigheid en UV-bestendigheid zijn superieur aan andere pijpen. Daarom kunnen met kunststof beklede stalen buizen op verschillende technische gebieden worden gebruikt. Afhankelijk van de verschillende omgevingen kunnen buizen van met kunststof bekleed staal verschillende prestatievoordelen uitoefenen.
De voordelen van het product zijn de hoge mechanische sterkte, geschikt voor ruwe gebruiksomgevingen; de binnenste en buitenste coatings kunnen metaaloxidatie voorkomen en hebben een goede weerstand tegen chemische corrosie. De coating heeft een sterke hechting, hoge hechtsterkte en goede slagvastheid. Lage coëfficiënt van oppervlakteruwheid en wrijvingscoëfficiënt, goede hechting aan vreemde stoffen; anti-veroudert, lange levensduur.
De met kunststof beklede stalen buis is een nieuw type buismateriaal dat de afgelopen jaren is ontwikkeld. De pijpleiding heeft met succes het verlies als gevolg van corrosie in de pijpleiding verminderd en behoort tot de groene energiebesparende pijpleiding. De drukvastheid, trekvastheid, corrosiebestendigheid en UV-bestendigheid zijn superieur aan andere pijpen. Daarom kunnen met kunststof beklede stalen buizen op verschillende technische gebieden worden gebruikt. Afhankelijk van de verschillende omgevingen kunnen buizen van met kunststof bekleed staal verschillende prestatievoordelen uitoefenen.
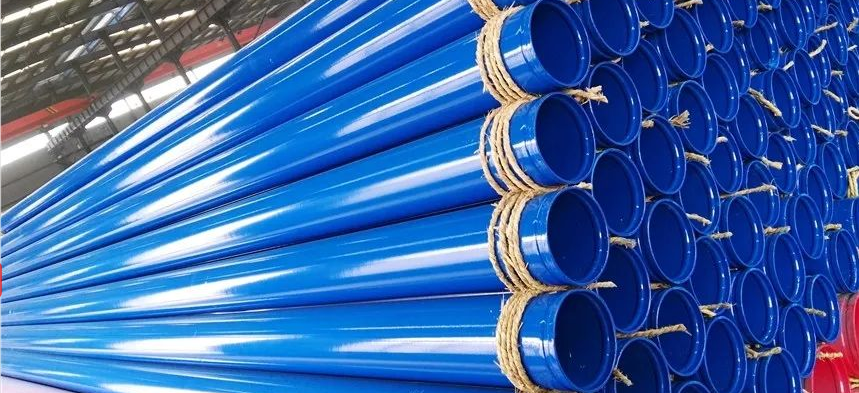