Was ist das Caustic Cracking in der Dampfpipeline?
Caustic Cracking, auch bekannt als Laugenversprödung, ist die Rissbildung von Metallen in alkalischen Lösungen durch die kombinierte Wirkung von Zugspannung und korrosiven Medien, ist eine Art von SCC. Die Ursache für die Rissbildung in Druckkesseln ist hauptsächlich in den Teilen zu finden, in denen Dampf wiederholt verdampft und kondensiert oder mit Natronlauge in Berührung kommt; dies können Kohlenstoffstahl, niedrig legierter Stahl, Ferritstahl und austenitischer Edelstahl sein. Unfälle mit Rissexplosionen ereignen sich häufig in Kesselanlagen, aber auch in Autoklaven, Abwärmerückgewinnungssystemen und Al2O3-Verdampfern von elektrolytischen Aluminiumunternehmen in Chloralkalichemieanlagen, Papierfabriken und in der Kernkraftindustrie.
Wenn die Natriumhydroxid-Konzentration mehr als 5% beträgt, ist es sehr wahrscheinlich, dass Kohlenstoffstahl und niedrig legierter Stahl in Dampfleitungen Laugenrisse bilden, alkalische Spannungskorrosion tritt im Allgemeinen bei mehr als 50~80℃ auf, besonders in der Nähe des Siedepunkts des Hochtemperaturbereichs, Alkalikonzentration von 40% ~ 50%. Nach der Theorie, wenn der Massenanteil der lokalen NaOH größer als 10% ist, wird die schützende Oxidschicht des Metalls aufgelöst werden, und die Matrix Metall wird mit dem Alkali weiter reagieren, um lose und poröse magnetische korrosive Oxide bilden, und die wässrige Lösung ist alkalisch. Solange 10~20mg-L-1 NaOH im Wasser von Kesseln oder Wärmetauschern enthalten ist, kann wiederholtes lokales Verdampfen zur Konzentration von Alkali unter dem Sediment oder in den Spalten führen, was lokale Alkalikorrosion verursacht.
Die Faktoren, die die Empfindlichkeit der Laugenrissbildung beeinflussen
Laugenrisse treten leicht in den konzentrierten Teilen von alkalihaltigen Flüssigkeiten mit hohen Eigenspannungen auf, z. B. in Schweißverbindungen. Diese Art von SCC entwickelt sich in der Regel intergranular und die Risse sind mit Oxiden gefüllt.
Die alkalisch-spröden Risse im Kohlenstoffstahl Dampfleitung erscheinen als feine intergranuläre Risse mit Oxiden. Es gibt mehrere Hauptfaktoren, die die Sprödigkeit von Alkali bestimmen: Alkalikonzentration, Metalltemperatur und Zugspannung. Experimente zeigen, dass einige Laugenrisse innerhalb weniger Tage auftreten, während die meisten Risse auftreten, wenn sie mehr als 1 Jahr lang ausgesetzt sind. Eine Erhöhung der Alkalikonzentration und der Temperatur kann die Rissbildungsrate verbessern.
Mittel
Laugenrissbildung ist die Korrosion, die bei hohen Temperaturen in konzentrierter Lauge auftritt. Wenn der Massenanteil von NaOH geringer als 5% ist, kommt es nicht zu Laugenrissbildung. Diese konzentrierte Lauge kann das Arbeitsmedium sein oder währenddessen gewonnen werden. Je höher die Konzentration der Natronlauge ist, desto größer ist die Empfindlichkeit der Laugenrissbildung, die nicht nur mit der Konzentration der Lauge zusammenhängt, sondern auch von der Temperatur der Lösung abhängt.
Die Temperatur
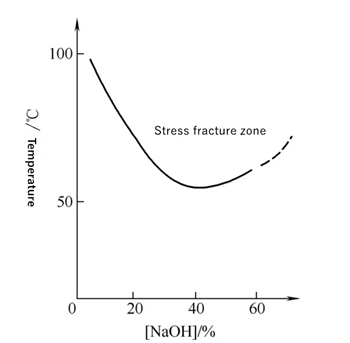
Die Rissbruchzeit von kohlenstoffarmen Dampfpipelinestählen nimmt mit der Abnahme der Spannung zu. Es wurde festgestellt, dass das Metall in der Wärmeeinflusszone mit der größten plastischen Restverformung, d. h. das Metall, das beim Schweißen auf 500~850℃ erhitzt wird, die größte SCC-Tendenz aufweist. Bei der Instandhaltung alkalischer Anlagen wurde festgestellt, dass die Metalle, die beim Schweißen auf Temperaturen über 550℃ und etwas unterhalb der Rekristallisationszone erhitzt wurden, in alkalischer Lösung, wo die Schweißeigenspannung und die Mikrostrukturspannung am größten sind, die größte Rissneigung aufweisen.
Metallische Elemente
Da die Laugenriss- und Nitratsprödigkeit von kohlenstoffarmen Stählen entlang des Korns gebrochen wird, wird angenommen, dass die Empfindlichkeit dieser Sprödigkeit durch die Entmischung von C, N und anderen Elementen an der Korngrenze verursacht wird. Die chemischen Elemente, die die Laugenrissigkeit von kohlenstoffarmem Dampfpipelinestahl verursachen, sind wie folgt:
C- und N-Entmischung an Korngrenzen erhöht die Laugenrissempfindlichkeit;
Die Auswirkung von Spurenelementen, die auf die Entmischung von S, P, As und anderen Verunreinigungen an den Korngrenzen zurückzuführen ist, erhöht die Empfindlichkeit gegenüber Alkaliversprödigkeit. Eine geringe Menge an La, Al, Ti und V kann jedoch dazu beitragen, die Ausscheidung schädlicher Verunreinigungen an der Korngrenze zu verringern und damit die Empfindlichkeit gegenüber Alkaliversprödigkeit zu reduzieren.
▪ Die Laugenrissbildung nimmt mit zunehmender Korngröße zu;
▪ Wärmebehandlung. Die Laugenrissempfindlichkeit des Stahls nach dem Sphäroidisieren ist größer als die des normalisierten Zustands, was auf die Zunahme der Korngrenzenseigerung während des Sphäroidisierens der Karbide zurückzuführen sein kann.
Potenzielle
Das empfindliche Potenzial der Laugenrissbildung von kohlenstoffarmem Dampfpipelinestahl in siedender 35%~40% NaOH-Lösung beträgt -1150~800mV (SCE), und das Potenzial der Laugenrissbildung liegt im Bereich von -700mV (SCE) am Siedepunkt (120℃). Bei dem kritischen Potenzial nimmt die Querschnittsschrumpfung der Probe stark ab. Die Röntgenstrukturanalyse zeigt, dass der Fe3O4-Schutzfilm auf der Oberfläche der Probe gebildet wird.