Wat zijn de caustische barsten in de stoomleiding?
Het bijtende Barsten, dat ook als bijtende verbrossing wordt bekend, is het metalen barsten in alkalische oplossingen toe te schrijven aan de gecombineerde actie van trekspanning en corrosieve media, is een type van SCC. De oorzaak het barsten van drukboiler komt hoofdzakelijk in de delen voor waar de stoom herhaaldelijk wordt verdampt en gecondenseerd of in contact met bijtende soda, die koolstofstaal, laag legeringsstaal, ferrietstaal en austenitisch roestvrij staalmateriaal kan zijn. Oorzaak kraken explosie ongevallen komen vaak voor in ketels systeem, ook veroorzaakt door Na + concentratie kan ook optreden in autoclaps, restwarmte terugwinning systemen en Al2O3 verdampers van elektrolytisch aluminium ondernemingen in chloor-alkali chemische fabrieken, papierfabrieken en kernenergie-industrie.
Wanneer de natriumhydroxideconcentratie hoger is dan 5%, zullen koolstofstalen en laaggelegeerde stalen stoompijpleidingen waarschijnlijk bijtende scheuren vertonen, treedt alkalispanningscorrosie over het algemeen op bij meer dan 50~80℃, vooral in de buurt van het kookpunt van het gebied met hoge temperaturen, alkaliconcentratie van 40% ~ 50%. Volgens de theorie, wanneer de massafractie van lokale NaOH groter is dan 10%, zal de beschermende oxidelaag van het metaal worden opgelost, en het matrixmetaal zal verder reageren met de alkali om losse en poreuze magnetische corrosieve oxiden te vormen, en de waterige oplossing is alkalisch. Zolang er 10~20mg-L-1 NaOH in het water van de boiler of warmtewisselaar zit, kan lokale herhaalde verdamping leiden tot de concentratie van alkali onder het sediment of in de spleten, waardoor lokale alkalicorrosie ontstaat.
De factoren die de gevoeligheid van caustisch kraken beïnvloeden
Bijtende scheurvorming treedt gemakkelijk op in de geconcentreerde delen van alkali-houdende vloeistof met hoge restspanning, zoals lasnaaddelen, dit type SCC ontwikkelt zich meestal interkristallijn en de breuken zijn gevuld met oxiden.
De alkalibrosse scheuren in het koolstofstaal stoomleiding verschijnen als fijne interkristallijne scheurtjes met oxiden. Er zijn verschillende hoofdfactoren die de brosheid van alkali bepalen: alkaliconcentratie, metaaltemperatuur en trekspanning. Experimenten tonen aan dat sommige bijtende scheuren binnen een paar dagen ontstaan, terwijl de meeste ontstaan bij blootstelling aan meer dan 1 jaar. Het verhogen van de alkaliconcentratie en de temperatuur kan de scheurvorming verbeteren.
Medium
Bijtende barstvorming is de corrosie die optreedt bij hoge temperaturen in geconcentreerde loog. Als de massafractie van NaOH lager is dan 5%, zal er geen bijtend kraken optreden. Deze geconcentreerde loog kan het werkmedium zijn of kan tijdens het proces worden verzameld. Hoe hoger de concentratie van natronloog, hoe groter de gevoeligheid van bijtende kraken, die niet alleen gerelateerd is aan de concentratie van de alkali, maar ook afhangt van de temperatuur van de oplossing.
De temperatuur
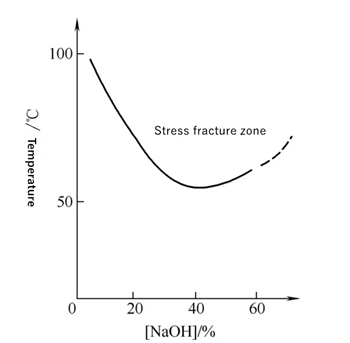
De scheurbreuktijd van staal voor stoomleidingen met een laag koolstofgehalte neemt toe met de afname van de spanning. Het blijkt dat het metaal in de warmte-beïnvloede zone met de grootste restplastische vervorming, dat wil zeggen het metaal dat tijdens het lasproces tot 500~850℃ wordt verhit, de grootste neiging tot SCC heeft. Bij het onderhoud van alkali-installaties bleek dat de metalen die tijdens het lassen bij temperaturen boven 550℃ en iets lager dan de herkristallisatiezone werden verhit, de grootste scheurneiging in alkalische oplossing hadden, waarbij de lasrestspanning en microstructuurspanning het grootst zijn.
Metalen elementen
Omdat het bijtende kraken en de nitraatbroosheid van koolstofstaal met een laag koolstofgehalte langs de korrel wordt gebroken, is de theorie dat de gevoeligheid van deze broosheid wordt veroorzaakt door de segregatie van C, N en andere elementen op de korrelgrens. De chemische elementen die het caustisch kraken van staal voor stoompijpleidingen met laag koolstofgehalte veroorzaken, zijn de volgende:
C- en N-segregatie bij korrelgrenzen verhoogt de gevoeligheid voor caustisch barsten;
Het effect van sporenelementen door de segregatie van S, P, As en andere onzuiverheden bij korrelgrenzen verhoogt de gevoeligheid voor alkalibrosheid. Een kleine hoeveelheid La, Al, Ti en V kan echter te wijten zijn aan het verminderen van de segregatie van schadelijke onzuiverheden in de korrelgrens waardoor de gevoeligheid voor alkalibrosheid afneemt.
Het bijtende kraken neemt toe naarmate de korrelgrootte toeneemt;
Warmtebehandeling. De gevoeligheid voor caustische scheurvorming van het staal na het sferoïderen is groter dan die van de genormaliseerde toestand, wat te wijten kan zijn aan de toename van de korrelgrenssegregatie tijdens het sferoïderen van de carbiden.
Potentieel
De gevoelige potentiaal van bijtende kraken van lage koolstof stoom pijpleiding staal in kokende 35% ~ 40% NaOH oplossing is -1150 ~ 800mV (SCE), en de potentiaal van bijtende kraken optreedt in het bereik van -700mV (SCE) bij het kookpunt (120 ℃). Bij de kritische potentiaal neemt de sectiekrimp van het monster sterk af. De röntgenstructuuranalyse laat zien dat de Fe3O4 beschermende film wordt gevormd op het oppervlak van het monster.