What’s the Caustic Cracking in the steam pipeline?
Caustic Cracking, also known as caustic embrittlement, is the metals cracking in alkaline solutions due to the combined action of tensile stress and corrosive media, is a type of SCC. The cause cracking of pressure boiler mainly occurs in the parts where steam is repeatedly evaporated and condensed or in contact with caustic soda, which may be carbon steel, low alloy steel, ferrite steel and austenitic stainless steel equipment. Cause cracking explosion accidents often occur in boilers system, also caused by Na+ concentration may also occur in autoclaps, waste heat recovery systems and Al2O3 evaporators of electrolytic aluminum enterprises in chlor-alkali chemical plants, paper mills and nuclear power industries.
When sodium hydroxide concentration is more than 5%, carbon steel and low alloy steel steam pipelines are almost likely to produce caustic crackings, alkali stress corrosion generally occurs at more than 50~80℃, especially near the boiling point of high temperature area, alkali concentration of 40% ~ 50%. According to the theory, when the mass fraction of local NaOH is greater than 10%, the protective oxide film of the metal will be dissolved, and the matrix metal will react with the alkali further to form loose and porous magnetic corrosive oxides, and the aqueous solution is alkaline. As long as 10~20mg·L-1 NaOH is contained in the water of boiler or heat exchanger, local repeated evaporation can lead to the concentration of alkali under the sediment or in the crevices, causing local alkali corrosion.
The factors affecting the sensitivity of caustic cracking
Caustic cracking is easy to occur in the concentrated parts of alkali containing liquid with high residual stress, such as welding joint parts, this type of SCC is usually developing intergranular and the fractures are filled with oxides.
The alkali-brittle cracks in the carbon steel steam pipeline appear as fine intergranular cracks with oxides. There are several main factors that determine the brittleness of alkali: alkali concentration, metal temperature and tensile stress. Experiments show that some caustic cracking occurs within a few days, while most occur when exposed to more than 1 year. Increasing the alkali concentration and temperature can improve the cracking rate.
Medium
Caustic cracking is the corrosion that occurs at high temperatures in concentrated lye. When the mass fraction of NaOH is lower than 5%, there won’t cause caustic cracking. This concentrated lye can be the working medium or can be gathered during. The higher the concentration of caustic soda, the greater the sensitivity of caustic cracking, which is not only related to the concentration of the alkali but also depends on the temperature of the solution.
The temperature
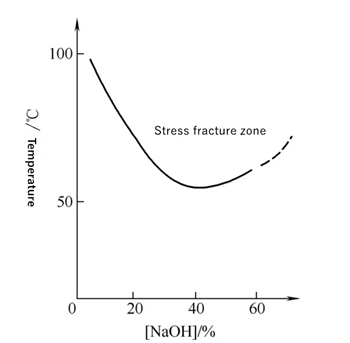
The cracking fracture time of low carbon steam pipeline steels increases with the decrease of stress. It is found that the metal in the heat-affected zone with the largest residual plastic deformation, that is, the metal heated to 500~850℃ in the welding process, has the largest SCC tendency. It was found in the maintenance of alkali equipment that the metals heated at temperatures over 550℃ and slightly lower than the recrystallization zone during welding had the greatest cracking tendency in alkaline solution, where the welding residual stress and microstructure stress are the largest.
Metal elements
Because the caustic cracking and nitrate brittleness of low carbon steel is fractured along the grain, it is theorized that the sensitivity of such brittleness is caused by the segregation of C, N and other elements at the grain boundary. The chemical elements that cause the caustic cracking of low carbon steam pipeline steel are as follows:
▪ C and N segregation at grain boundaries increases the caustic cracking sensitivity;
▪ The effect of trace elements, due to the segregation of S, P, As and other impurities at grain boundaries increase alkali embrittlement sensitivity. However, a small amount of La, Al, Ti and V may be due to reducing the segregation of harmful impurities in the grain boundary reducing the alkali embrittlement sensitivity.
▪ The caustic cracking increases as grain size increase,;
▪ Heat treatment. The caustic cracking sensitivity of the steel after spheroidizing is greater than that of the normalized state, which may be due to the increase of grain boundary segregation during the spheroidizing of carbides.
Potential
The sensitive potential of caustic cracking of low carbon steam pipeline steel in boiling 35%~40% NaOH solution is -1150~800mV (SCE), and the potential of caustic cracking occurs in the range of -700mV (SCE) at boiling point (120℃). At the critical potential, the section shrinkage of the sample decreases greatly. The X-ray structure analysis shows that the Fe3O4 protective film is formed on the surface of the sample.